3 Ways Healthcare Asset Tracking Improves Preventive Maintenance
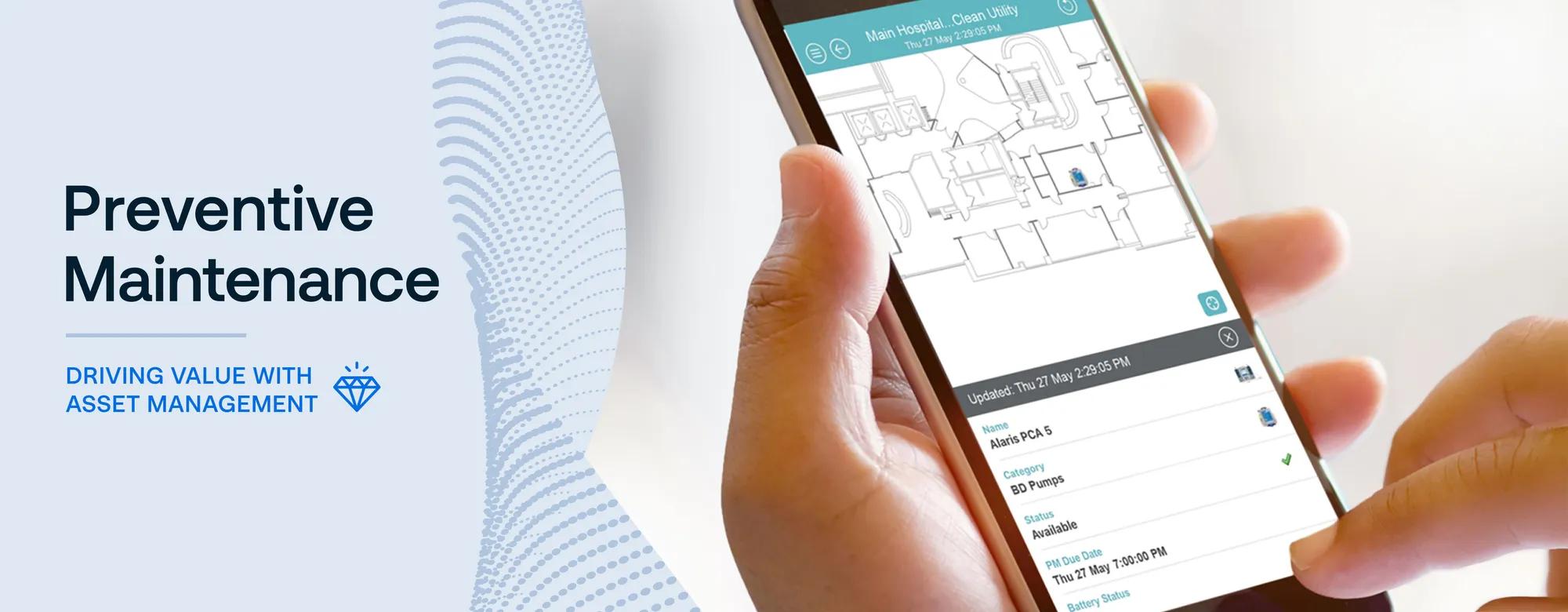
How many hours do your clinical engineers spend searching for equipment that’s due for maintenance? Discover how healthcare asset tracking can change the equation.
Every type of clinical equipment needs preventive maintenance. That typically occurs in huge, overlapping cycles. It also requires significant time and effort of your biomedical/clinical engineering personnel.
Because many medical assets are highly mobile, simply locating every piece of equipment can be one of the biggest challenges for preventive maintenance.
The time spent hunting for healthcare assets also drains your organization of one of its most vital resources: clinical engineering time. Wasted time and frustrated workers aren’t the only things that can occur when assets are difficult to find. Patient safety can be impacted, as well.
Improving Preventive Maintenance with RTLS
When a hospital implements a Real-time Location System (RTLS) solution for healthcare asset tracking, clinical engineering staff can locate every tagged asset easily and accurately. Preventive maintenance can be completed in a timely and efficient manner.
Here are 3 simple yet powerful ways RTLS-enabled healthcare asset management can help you improve your approach to preventive maintenance:
1. Automate equipment locating
Having visibility to the real-time location of tagged assets drastically reduces the time it takes to locate and retrieve equipment for preventive maintenance (PM). Instead of physically rounding a facility until equipment has been located, your staff can quickly and efficiently find the assets they are searching for within the hospital or across the campus.
Taking it a step further, the RLTS system can be set up to proactively alert staff when a PM due date is approaching. In addition, favorite searches can be created to quickly locate groups of equipment with a business status of “Due for PM” to further improve staff efficiency.
2. Integrate with your CMMS
To maximize effectiveness, healthcare facilities are leveraging integrations between an RTLS platform, clinical systems and medical device software. One of the most common integrations is with a computerized maintenance management system (CMMS). Such an integration allows for seamless data management to assist in preventive maintenance—adding location context to the CMMS native platform.
3. Integrate with your infusion pumps
Another best practice is to integrate to infusion pumps. This integration makes it possible to provide device status to the RTLS solution, helping clinical engineering understand when pumps are available for maintenance and avoid in-use devices. The real-time insight allows staff to streamline workflows and save time by strategically mapping out asset retrieval.
Learn How One Hospital Used RLTS to Achieve 100% Preventive Maintenance Annually
Leaders at Saint Francis Medical Center saw the value in using a comprehensive RTLS platform. With BD Alaris™ Asset Management interface of the BD Alaris™ System with Securitas Healthcare RTLS platform, the hospital now has real-time visibility to the location of every infusion device. In addition, the platform integration makes it possible to know the device status: ON/OFF, Available, In-Use.
As a result, Saint Francis has improved workflow, device utilization and staff efficiency. They were able to double their infusion device fleet without adding additional staff. Get the specifics on how this medical center used RTLS-powered healthcare asset management to reduce equipment and maintenance costs and achieve 100% preventive maintenance every year. In addition, the team now completes drug library updates in just three weeks, which used to take a full year.
Read more about additional asset management advanced use cases.